Laser Cut Perforated 6061 Aluminium Plate
Specifications of 6061 Laser Cut Plate |
Laser cutting perforated 6061 aluminum plates is a common manufacturing process used to create precise patterns of holes or other shapes in aluminum sheets. 6061 aluminum alloy is a versatile material known for its excellent strength-to-weight ratio, corrosion resistance, and weldability, making it suitable for various applications across industries such as aerospace, automotive, and electronics.Perforated aluminum plates find applications in various industries, including architectural design, filtration systems, decorative panels, and aerospace components.
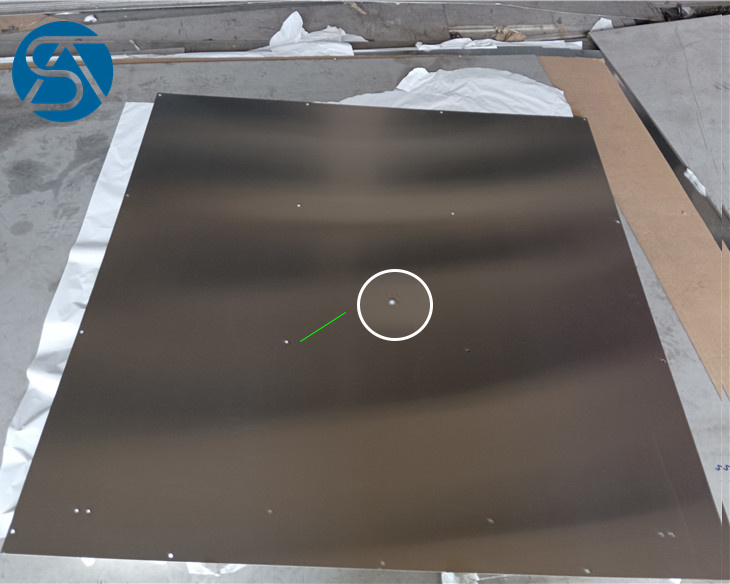
Standards | ASTM B209 / ASME SB209 |
Thickness | 0.2-50mm |
Width | 100-2600mm |
Length | 500-10000mm |
Temper | O,H12,H14,H16,H18,H19,H22,H24 |
Technology | Cutting,Perforated |
6061 Perforated Sheet Equivalent Grades : |
Grade | UNS | USA | WNR | EN | DIN | ISO | BS |
6061 | A96061 | AA6061 | 3.3211 | AW-AlMg1SiCu
EN AW-6061 |
AlMgSiCu | AlMg1SiCu | HE20 |
6061 Aluminium Plate Chemical Composition: |
Grade | Fe | Si | Mg | Mn | Cu | Zn | Ti | Cr | Al | Others |
6061 | 0.7 | 0.4-0.8 | 0.8-1.2 | 0.15 | 0.15-0.4 | 0.25 | 0.15 | 0.15-0.35 | Remainder | 0.005/0.15 |
Mechanical Properties of 6061 Aluminum Plates & Sheets: |
Grade | Density | Tensile Strength | Hardness Brinell | Hardness Rockwell | Yield Strength | Fatigue Strength | Shear Strength |
6061 | 2.7 g/cc | 310MPa | 95 | B60 | 276Mpa | 96.5 MPa | 207 MPa |
Laser cutting offers several advantages for perforating aluminum plates, including: |
1.Precision: Laser cutting allows for very precise cuts and hole patterns, enabling intricate designs and tight tolerances to be achieved.
2.Versatility: Laser cutting can create a wide range of hole sizes, shapes, and patterns, depending on the requirements of the application.
3.Speed: Laser cutting is a fast and efficient process, capable of perforating aluminum plates quickly and accurately.
4.Clean edges: Laser cutting produces clean, burr-free edges, minimizing the need for additional finishing processes.
What are the differences between laser cutting and plasma cutting? |
The main difference between laser cutting and plasma cutting is the difference in cutting thickness, and of course the difference in cutting operating costs. The advantage of plasma cutting is that it can cut thick plates and is cheap, but the surface of the cut material is rough. Laser cutting has a smooth surface and high cutting accuracy, but is more expensive than plasma cutting. The disadvantage of plasma cutting is that the cutting gap is large, about 3MM. The most important component of plasma is the power supply. In fact, compared to the laser of the laser cutting machine, the power consumption of plasma is very large.
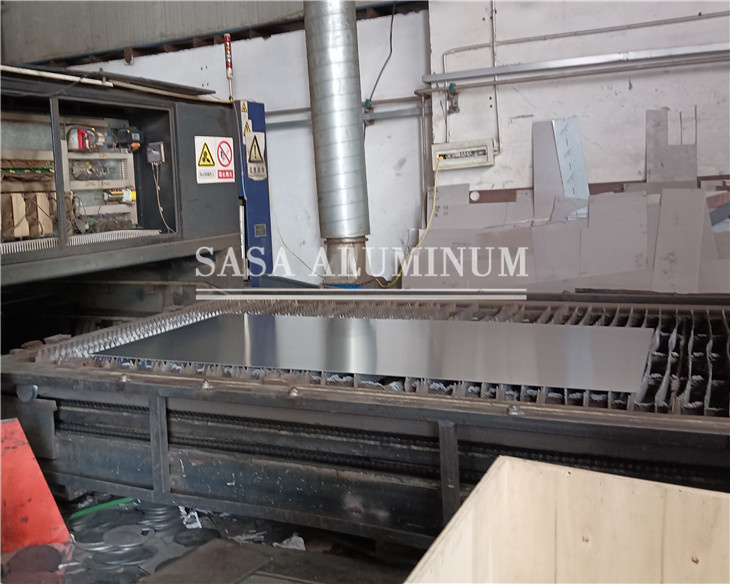
Plasma cutting machine is a kind of thermal cutting equipment. The main working principle is compressed air as the main body and high-temperature and high-speed plasma arc as the heat source. It locally melts the metal being cut and blows away the melted metal with high-speed airflow at the same time. Create a narrow slit. Plasma cutting machines can cut various metal materials such as stainless steel, iron, aluminum, and copper with fast cutting speed, narrow slits, and smooth cuts. Plasma cutting machines are generally used in the construction, installation and maintenance of machinery and metal structures.
Laser cutting machines use high-power and high-density laser beams to scan the surface of materials. They can heat the materials to thousands or even tens of thousands of degrees Celsius in a short time, melt or vaporize the materials, and then use high-pressure gas to melt or vaporize the materials. Other materials are blown away from the cuts. Laser cutting uses an invisible beam to replace the traditional mechanical knife. The laser cutting speed is fast and the incision is smooth. Generally, no post-processing is required. The cutting is less affected by heat and the plate deformation is small.
The difference in cutting accuracy is that plasma cutting accuracy can reach within 1mm, while laser cutting accuracy can reach within 0.22mm. In terms of cost, plasma cutting machines are cheaper than laser cutting machines. In terms of processing accuracy, plasma cutting is equivalent to rough processing, and laser cutting is equivalent to fine processing.
Our Services: |
1.Quenching and tempering
2.Vacuum heat treating
3.Mirror-polished surface
4.Precision-milled finish
4.CNC machining
5.Precision drilling
6.Cut into smaller sections
7.Achieve mold-like precision
SASA Aluminum's Packing: |
1. Packing is quite important especially in a case of international shipments in which consignment pass through various channels to reach the ultimate destination, so we put special concern regarding packaging.
2. Sasa aluminum's pack our goods in numerous ways based on the products. We pack our products in multiple ways, such as,
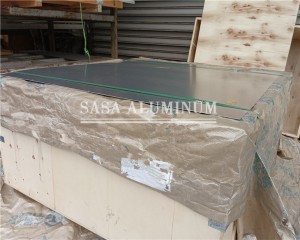
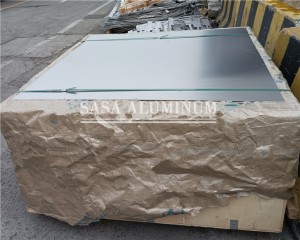
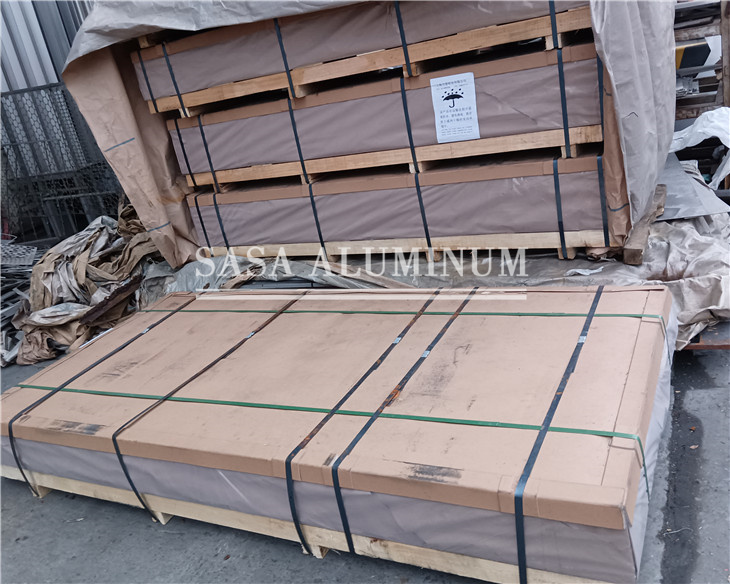